- Home
- Page
Design Guide Line
There are many different printers available, only nine basic types of 3D printing technology currently exist:
- Stereolithography (SLA),
- Digital Light Processing (DLP),
- Selective Laser Sintering (SLS),
- Selective Laser Melting (SLM),
- Electron Beam Melting (EMB),
- Laminated Object Manufacturing (LOM),
- Binder Jetting (BJ),
- Material Jetting/Wax Casting.
- Fused Deposition Modelling (FDM),
- Stereolithography (SLA),
- Digital Light Processing (DLP),
- Selective Laser Sintering (SLS),
- Selective Laser Melting (SLM),
- Electron Beam Melting (EMB),
- Laminated Object Manufacturing (LOM),
- Binder Jetting (BJ),
- Material Jetting/Wax Casting.
- Fused Deposition Modelling (FDM),
FDM is the most common form of desktop 3D printing in the consumer market. The FDM system consists of a platform extrusion nozzle and a control system that provides a quick and straightforward solution to 3D printing. The thermoplastic filament is heated and deposited in x and y coordinates as the object is built layer-by-layer in a z-direction. ccb@bobcards.comThis form of 3D printing is the most cost-effective way for individuals and small businesses to create parts quickly and efficiently. The printers have evolved from bulky, expensive machines to smaller, faster, economical ones that have become the key components for engineering and design departments.
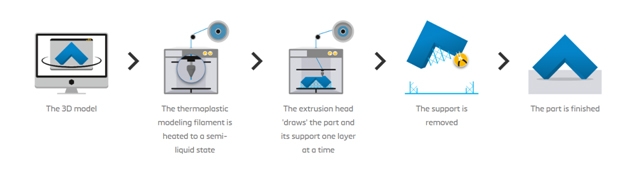
FDM Advantages
- FDM is a cheap and accessible 3D technology. This makes it perfect for beginners to 3D printing. It’s also the most commonly used rapid prototyping technology due to its ease of access.
- The technology is simple to use, and printers are often user-friendly. This is because FDM is mostly a consumer rather than industrial process so effort is made to make the 3D printers easy to use.
FDM Disadvantages / FDM Limitations
- The print quality of FDM / FFF 3D prints are not as good as those by SLA or SLS.
- 3D printing with fused deposition modelling is slow. This makes it unusable in some industries when large numbers of parts are needed quickly.
- The layer-by-layer printing in FDM can sometimes lead to problems with warping and minor shrinking.
Common FDM Materials
One of the key strengths of FDM is the wide range of available materials. These can range from commodity thermoplastics (such as PLA and ABS) to engineering materials (such as PA, TPU, and PETG) and high-performance thermoplastics (such as PEEK and PEI).
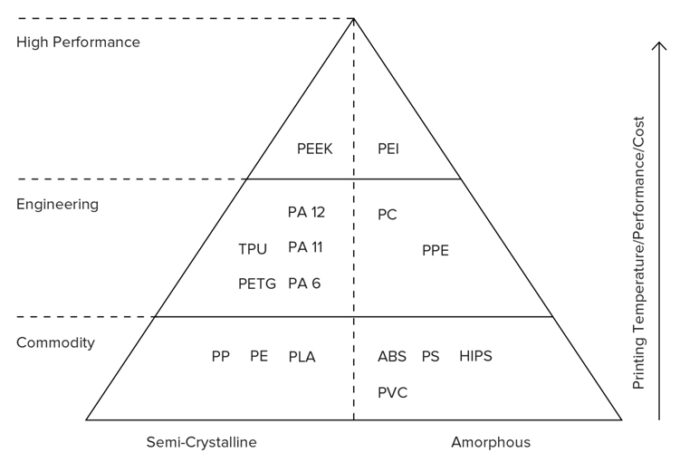
SLA – Stereolithography
The oldest additive printing technology is SLA. This form of 3D printing works by exposing a layer of photosensitive liquid resin to a UV-laser beam. The resin hardens in the desired pattern, and the object is built one layer at a time. DLP printing mimics the functions of an SLA printer with the main difference being it cures resin using a digital projector and light. A downfall of SLA printing is that the object must be rinsed with a solvent after the printing completes, and even at times has to bake in a UV light to finish the curing process.
Ideal applications for Stereolithography:
- Visual prototypes for photo shoots and market testing
- “Show and tell” parts with smooth surfaces and fine details
- Prototypes for limited functional testing
- Masters for copying techniques such as Vacuum Casting
- Alternatives for sheet metal prototypes when coated with a metal plating process
- Patterns for investment casting
- Low-volume production of complex geometries
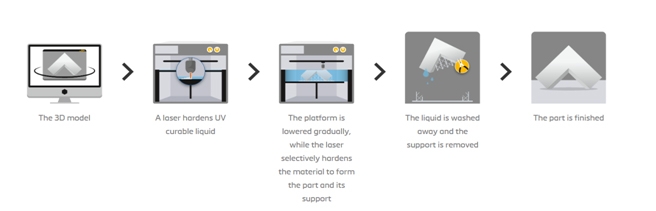
Why choose Laser Sintering?
Silicone molding results in high-quality parts comparable to injection-molded components. This makes vacuum casted models especially suitable for fit and function testing, marketing purposes or a series of final parts in limited quantities. Vacuum Casting also lends itself well to a variety of finishing degrees, and we can match the finish you need for your parts.
Ideal applications for Vacuum Casting
- Pre-launch product testing
- Small series of housings and covers
- Concept models and prototypes
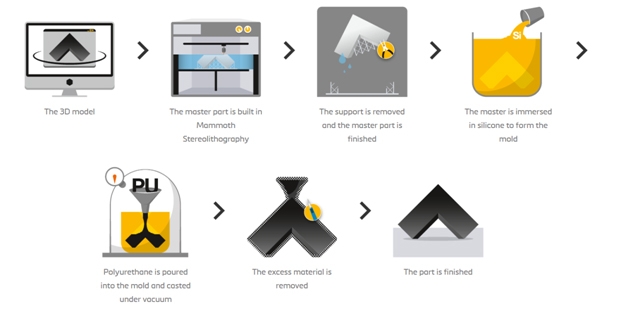
Contact Info
- 12, Mansarovar, Near Gaushala Circle, A.K. Road, Surat-395010
- (+91) 94279 77505
- info@3dtechno.in